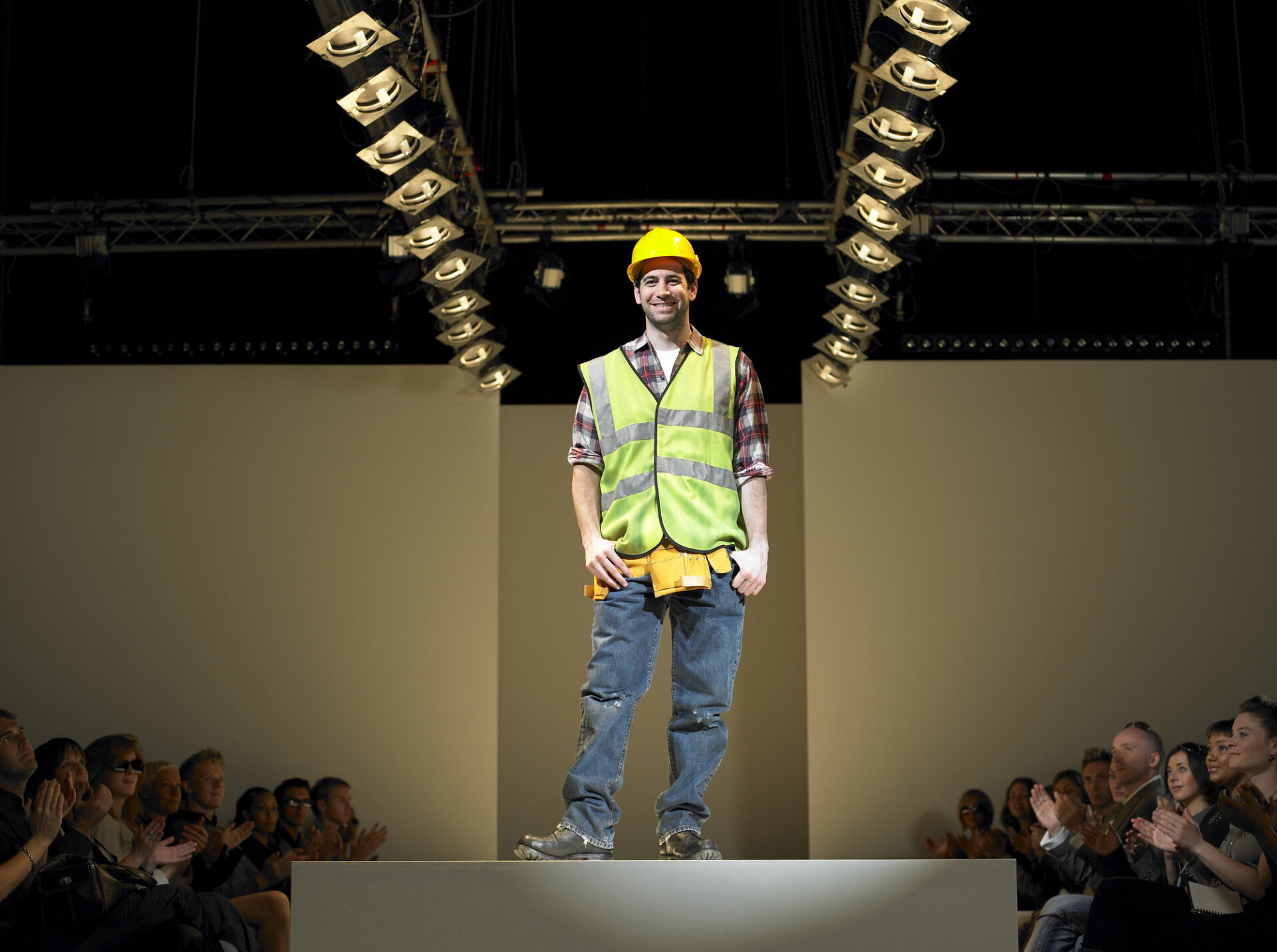
How to lose the show but keep the sticky
by Garrison Wynn, CSP
If you attend safety conferences, I hope you are hearing about the connection between employee engagement and safety. I introduced the concept in 2002 to about 2,500 oil and gas industry leaders and safety professionals when I spoke at a Chevron event in Salt Lake City. In truth, I was just applying the findings of a large Gallup leadership study I’d encountered earlier that year, drawn from plant location surveys that showed the link between an engaged workforce, awareness and a reduction in recordable incidents. The findings resonated with me. With a background in instrumentation, I had seen firsthand in chemical plants what was working and what was simply just “safety theater.” Since then, before and after the pandemic, I’ve interviewed thousands who say the leaders who make sure their people feel valuable have the fewest incidents and the most buy-in for their safety programs.
Let’s begin by defining safety theater as things that make people feel safe or give the appearance of a big safety effort but do very little to create a culture of safety. For example, fancy signage, 20-step processes and improved equipment look good from the outside but have little effect on human behavior and belief. If anything, these safety theater elements might give a false sense of security.
Sure, showing the world you are all about safety can help reduce the impact of lawsuits and make younger job seekers more interested. (Research shows that safety concerns are the top reason people under 30 years old don’t want industrial jobs.) But projecting your reputation for safety consciousness does not actually help enough to make the big difference you are looking for. Below are three things we know create a sustainable culture of safety, without the theatrics.
1. Relationships. People who know each other and talk to each other have a higher level of awareness as a team; they watch each other’s backs and have much less of a problem saying “Hey, Jimmy, that’s not the safe way to do it!”
2. Direct supervisor buy-in. If the people who directly manage those doing potentially hazardous work do not 100% believe in your safety polices, you do not have a safety culture — regardless of any other factor, process or situation.
3. Avoiding too much change. What I’m about to say may seem like sacrilege in our “all about change” work culture, so brace for it: When you keep changing the safety program, direct supervisors, especially since COIVD, become hesitant to buy into and teach something that will quickly become obsolete. I liken this to repeated cellphone updates that make you just want to throw the phone away.
A safety culture that sticks rests on a few key conditions. Make sure people know, trust and listen to each other. Get your direct supervisors to believe in your safety initiatives. And have a good safety foundation that you can tweak without making it brand-new all the time. Programs that are a bit tricky to explain or programs based on fixing the nonhuman elements just do not have enough impact. So avoid the tricky and embrace the sticky!
Safety Programs: https://www.motivational-speaker-success.com/topics/safety/